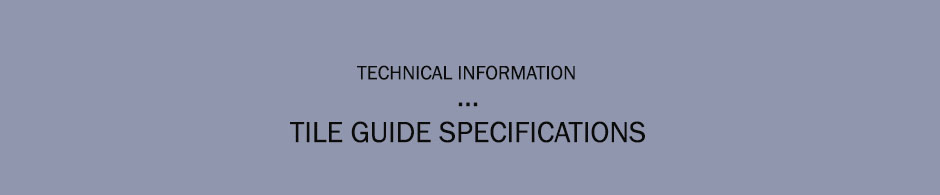
TILE GUIDE SPECIFICATIONS
PART 1 GENERAL
1.1 SUMMARY
A. Furnish materials, labor, transportation, services, and equipment necessary to furnish and install Quartz Tiles as indicated on drawings and as specified herein.
1.2 REFERENCES
A. American Society of Testing Materials (ASTM):
1. ASTM C-170
2. ASTM C-97
3. ASTM C-880
4. ASTM C241
5. ASTM C1028
6. RD2234
B. Performance Requirements
1. Compressive Strength at the time of delivery to be not less than 30,000 psi; averaging 32,000 psi when tested in accordance with ASTM C-170.
2. Water Absorption shall not be greater than 0.02%, when tested in accordance with ASTM C-97.
3. Flexural Strength shall not be less than 7000 psi average when tested in accordance with ASTM C-880.
4. Static Coefficient of Friction ASTM C-1028 conditionally slip resistant:
a. Wet: 0.41 – 0.71 depending on finish
b. Dry: 0.79 – 0.77 depending on finish
1.3 QUALITY ASSURANCE
A. Manufacturer: Company specializing in the manufacture of Quartz engineered stone.
B. Installation shall be by a contractor and crew with at least (1) year of experience in working with Quartz Tile & Slab.
C. Installation Contractor shall conform to all local, state/provincial licensing and bonding requirements.
1.4 SUBMITTALS
A. Submit installation instructions as recommended by European surfaces. B. Submit sample sets of units to indicate color and finish selections. Color & finish will be selected by Architect / Designer / Owner from manufacturer’s available colors, EuroStone Los Angeles, CA.
1.5 PROJECT CONDITIONS
A. Do not install tiles during heavy rain or snowfall.
B. Environmental Temperature must be between +5 C and +30 C.
C. The humidity of the foundation must be less than 3%.
1.6 PRODUCT DELIVERY, STORAGE AND HANDLING
Packaging and Shipping: Tiles (12″x12″, 12″x24″, 16″x16″) to be boxed in lots of 6-10, delivered in original unopened packaging with legible manufacturer identification, including size, quantity, manufacture date and inspector initials. Larger sizes individually strapped in crates or A-frames and spun wrapped. Storage: Store in dry, covered area.
1.7 WARRANTY
Manufacturer/Installer shall warrant installed system for a period of one year from date of substantial completion against failure of workmanship and materials.
1.8 MAINTENANCE
Extra Materials: Deliver supply of maintenance materials to the owner. Furnish maintenance materials from same lot as materials installed, and enclosed in protective packaging with appropriate identifying labels. Furnish not less than 1 percent of total product installed maintenance stock for each type, color, pattern and size of tile product installed.
PART 2 – PRODUCTS
2.1 Quartz Tiles
A. Manufacturers
1. Acceptable Manufacturer
EuroStone, Los Angeles, CA, (310)967-8000 www.eurostone.us
2.Drawings and installation specifications are based on manufacturer’s proprietary literature from EuroStone. Other manufacturer’s shall comply with the minimum levels of material specifications and detailing indicated on the drawings or specified herein.
2.2 MATERIALS
A. Crushed Quartz
B. Silica Sand
C. Resin Binder
D. Pigments
E. Various recycled materials
F. Sealer: Colorless, slip and stain resistant penetrating made specifically for Quartz surfacing.
2.3 MANUFACTURED UNITS
A. Tiles in Thickness of 1 Cm (3/8″ nominal)
1. Sizes:
a. 30×30 Cm (12″x12″ nominal)
b. 30×60 Cm (12″x24″ nominal)
c. 40×40 Cm (16″x16″ nominal)
d. 60×60 Cm (24″x24″ nominal)
e. 60×120 Cm (24″x48″ nominal)
f. 30×120 Cm (12″x48″ nominal)
g. 120×120 Cm (48″x48″ nominal)
2. Prepolished, chamfered edges, calibrated and squared.
3. Finish: Polished or Grain finish (honed).
4. Color: (From Eurostone color chart.)
2.5 FABRICATION
A. Mechanically vibrated in the molds.
B. Hydraulically pressed under vacuum.
C. Cured in heat chambers.
D. Factory finish: In-line grinding and polishing.
PART 3 – EXECUTION (THINSET METHOD)
3.0 EXAMINATION
A. Inspect foundation areas to receive tile for:
- Defects, cracks in existing work that affect proper execution of tile installation. Foundation must be absolutely dry, stable, solid, resistant to compression, and free of dust, grease, wax, paint and anything else that may impair adhesion. Foundation must be sufficiently mature. The maturity is calculated as about 6-8 days per Cm of thickness unless special quick-drying cements are used.
- Variances beyond allowable tolerances. Maximum variation in subfloor not to exceed 1/8″ in 10’0″ from required plane.
- Foundation moisture must be within acceptable industry limits. Excessive foundation moisture cannot escape through quartz material and may therefore cause detachment and warping.
3.1 INSTALLATION
A. Thinset application
- Apply latex cement mortar, conform with ANSI A118.4 utilizing a 3/8″ x 1/4″ square notch trowel. Use Two component Granirapid Mapei (or similar, Laticrete, Kerakoll etc.) made up of component A (bag of powder) and component B (thin of latex). Follow the manufacturer’s instruction to obtain the correct mix.
- Apply thin set for a minimum of 1/8″ setting bed. Allow for thinset manufacturers’ recommended setting time before grouting.
- Coat underside of each unit with latex cement mortar, firmly set, tamp into bedding to ensure minimum 95% surface contact with mortar bed.
- All units to be installed level, square, parallel, except where otherwise indicated in a true plane with adjacent units and other floor finishes.
- Maintain a 2-3 mm joint for smaller tiles and 4-5 mm joint for larger units.
B. Control Joints
- Over all structural expansion joints 2. All perimeter edges to have soft joints.
END OF SECTION